Modernization of direct current systems and prerequisites for rectifier replacement.
The existing AEG Profitec S direct current systems are designed to supply power to operational protection circuits and control technological equipment at a constant voltage of 125V and 220V. These systems were installed in 1999-2000 and have demonstrated high reliability and ease of maintenance over more than 20 years of service.
Unfortunately, as of 2021, the AEG Profitec S DC UPSs were not only discontinued but also lacked service support due to a shortage/lack of spare parts. The required radio components were unavailable due to obsolescence and production discontinuation. The use of new radio components would require redesigning, production setup, a complete testing cycle, and re-certification. Modern radio electronic components have undergone significant changes in terms of size and physical characteristics.
Decision from "MEK-Astana" LLP
Our company proposed the replacement of three sets of rectifiers (dual redundancy 1+1) with minimal possible changes to the existing power supply system of the facility. To achieve this, the equipment supply project for Tengizchevroil, created in the 90s, was retrieved from the technical archive of AEG Power Solution. Based on this project, AEG Power Solution developed a new technical solution that took into account all the features and options used in the twenty-year-old supply. Important aspects such as dimensions, mounting points, heights, and the placement of control elements and cable connection points were considered – in other words, everything possible was done to ensure compatibility between the new equipment and the systems from two decades ago. It was decided not to change the distribution cabinets, which avoided load disconnection and reduced the project timeline.
The proposed "hybrid" solution - new rectifiers + existing distribution cabinets and voltage reduction blocks - increased the reliability of the direct current systems, reduced operational expenses related to repairs and spare parts procurement, and allowed for a quick replacement process. The scope of the proposed supply also included the following services:
- Complete documentation package;
- Factory acceptance tests (FAT);
- Preparation and coordination of the work plan;
- Installation and commissioning;
- On-site testing;
- Training of the customer's personnel;
- Provision of software for the customer's personnel.
Project Implementation
Highly qualified specialists from "MEK-Astana" LLP, who have received the necessary training and have experience working with AEG Power Solution's direct current systems, were involved in the project.
For the most identical replacement, the AEG Protect RCS TPRe rectifier was selected. AEG Protect RCS is a thyristor-controlled rectifier suitable for charging lead-acid or nickel-cadmium battery packs while simultaneously supplying direct current loads. It is also permissible to use Protect RCS as a direct current power source without battery packs.
The rectifier has a service life of at least 20 years, and service support and spare parts sales are guaranteed for at least 10 years from the date of equipment sale. The production and factory acceptance tests of the rectifiers were carried out at the AEG PowerSolutions Iberica S.A plant in Vitoria, Spain.
The factory acceptance tests of the AEG Protect RCS TPRe rectifiers were conducted from March 25th to 28th, 2022. After receiving approval from the client, the equipment was packed according to international standards for maritime transport.
Despite the gradual easing of COVID-19 restrictions worldwide after two years of the pandemic, global logistics still face risks due to COVID-19. The events in Ukraine have become a new serious challenge for global transportation, resulting in many transportation companies and freight vehicles losing the right to cross the borders of the European Union or the Republic of Belarus. This situation has caused significant difficulties in delivering equipment to the Republic of Kazakhstan, including increased documentation, delivery time, and cost. Moreover, transportation disruptions have also been observed in Europe itself (weather conditions, driver strikes, etc.).
Due to the challenging situation, we made the decision to transport the equipment by air to Atyrau. Thanks to the coordinated work of the logistics department, we managed to avoid major delays and complete the installation work within the allocated timeframe.
During the production of the rectifiers, our company developed a detailed plan for the replacement of the existing rectifiers. The production plan met the client's requirements and ensured maximum safety for all personnel involved in the work. The replacement of the direct current systems at the client's facilities was carried out strictly according to the production plan without load disconnection and consisted of the following stages:
1. Unpacking and inspection of new AEG Protect RCS TPRe rectifiers.
2. Preparatory work, verification of rectifier compliance with drawings and schematics, and making additional changes according to the specifications.
3. Removal of the existing AEG Profitec S A rectifier, installation of the new AEG Protect TRRe A rectifier.
4. Startup of the installed rectifier, configuration, and parallel operation.
5. Removal of the existing AEG Profitec S B rectifier, installation of the second AEG Protect TRRe B rectifier.
6. Startup of the installed rectifier, configuration, and parallel operation.
7. Conducting functional tests on each direct current system (Site Acceptance Test).
8. Verification of relay signaling operation.
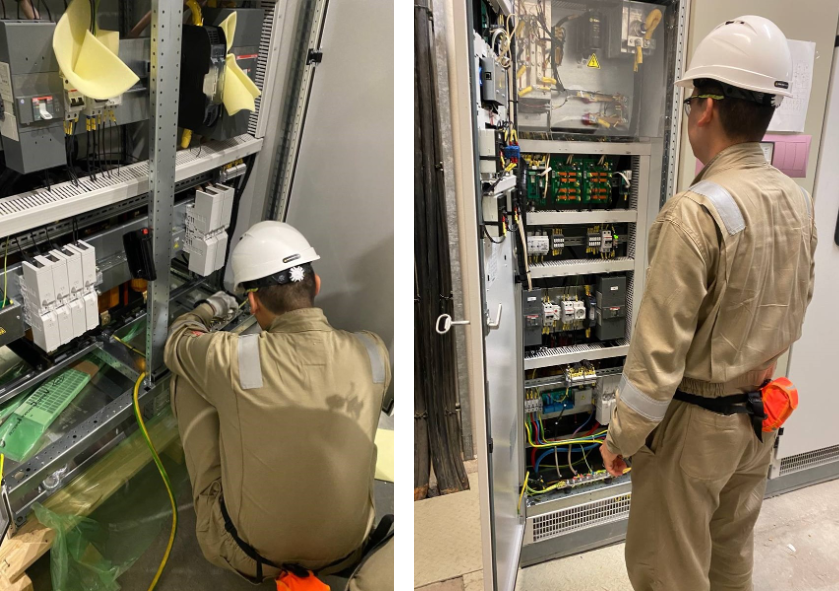
The replacement of the rectifiers was carried out during planned maintenance work at the client's facilities in June 2022. It was crucial to meet the required dates to avoid disruptions in the technological processes. Our company's engineers arrived at the site to supervise the installation work and perform commissioning activities, followed by the rectifiers' operation at 125V and 220V.
Thanks to the coordinated work of the subcontractor's specialists, the client's operational staff, and the technical department of MEK-Astana, delays were avoided, and the replacement of six rectifiers was completed within 14 calendar days. During the work, our specialists provided the following services:
- Supervision of equipment removal and installation.
- Commissioning of the new rectifiers.
- Testing to ensure proper functioning of all control units.
- Inspection of all nuts, bolts, screws, and connecting elements for tightening torque and color changes during heating.
- Calibration and registration of data for all electronic devices according to the technical requirements of the system.
- Testing of emergency signaling functions.
- Load testing, step load testing, discharge/charge testing of battery packs.
- Equipment functionality testing and verification under different operating modes: normal mode, battery pack mode, battery charging mode.
- Verification and configuration of spare parts included in the rectifier supply for two years of operation.
- On-site training of the client's technical personnel during the work execution.
Project Summary
To update the direct current systems at the client's facilities, efficient and reliable rectifiers from the same manufacturer, AEG Power Solutions, were selected. These rectifiers fully meet the client's demanding reliability requirements and are a long-term or permanent choice. AEG is a choice for the long run! Thanks to the well-chosen solution, the following achievements were realized:
- Restoration of a high level of equipment reliability and stability.
- Preservation of the principles and methods of working with the equipment, without requiring changes to the client's core competencies.
- Minimal construction impact on the work sites.
- Extension of the service life of the direct current power systems by an additional 10-15 years.
- The work needs to be carried out according to a detailed work production plan that pre-calculates any risks.
- Modernization of an existing facility is a much more complex process than constructing a new facility from scratch. Such work is impossible without the involvement of highly skilled specialists.
- The symbiosis between the professional integrator, MEK-Astana LLP, and the mature, established global manufacturer, AEG Power Solutions, enables the resolution of almost any client's tasks.
We hope that our cooperation with Tengizchevroil LLP will continue and be long-lasting and fruitful.
The MEK-Astana team fulfills all client requirements, guarantees a professional approach from its specialists to any issue, utilizing the most advanced equipment and technologies, as well as a comprehensive approach to implementing projects of any scale and complexity.
R. Smagulov, Account Manager
A. Musevich, Pre-Sales Engineer
MEK-Astana LLP
- Comments